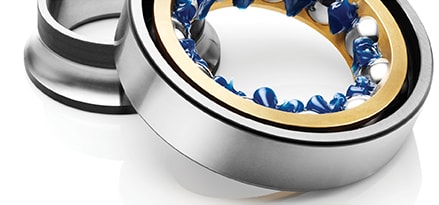
Determining relubrication intervals
Rick Russo, Product Technical Advisor, ExxonMobil Research and Engineering
Determining Relubrication Intervals
Rolling element bearings need to be relubricated from time to time to replace grease that has deteriorated, leaked away or become contaminated. However, because the conditions under which rolling element bearings operate can vary so widely, it requires on-the-spot know-how to determine proper relubrication intervals.
How often should I relubricate?
Unfortunately, there is no single answer to this question. This diagram is valid for bearings on horizontal shafts, in stationary machines, operating under normal loads and at a temperature not exceeding 71.1°C (160°F).
Scale a: Radial ball bearings
Scale b: Cylindrical roller bearings, needle roller bearings
Scale c: Spherical roller bearings, taper roller bearings, thrust ball bearings, full complement cylindrical roller bearings (20% relubrication interval hours of operation), crossed cylindrical roller bearings with cage (30% relubrication interval hours of operation), cylindrical roller thrust bearings, needle roller thrust bearings and spherical roller thrust bearings (50% relubrication interval hours of operation)
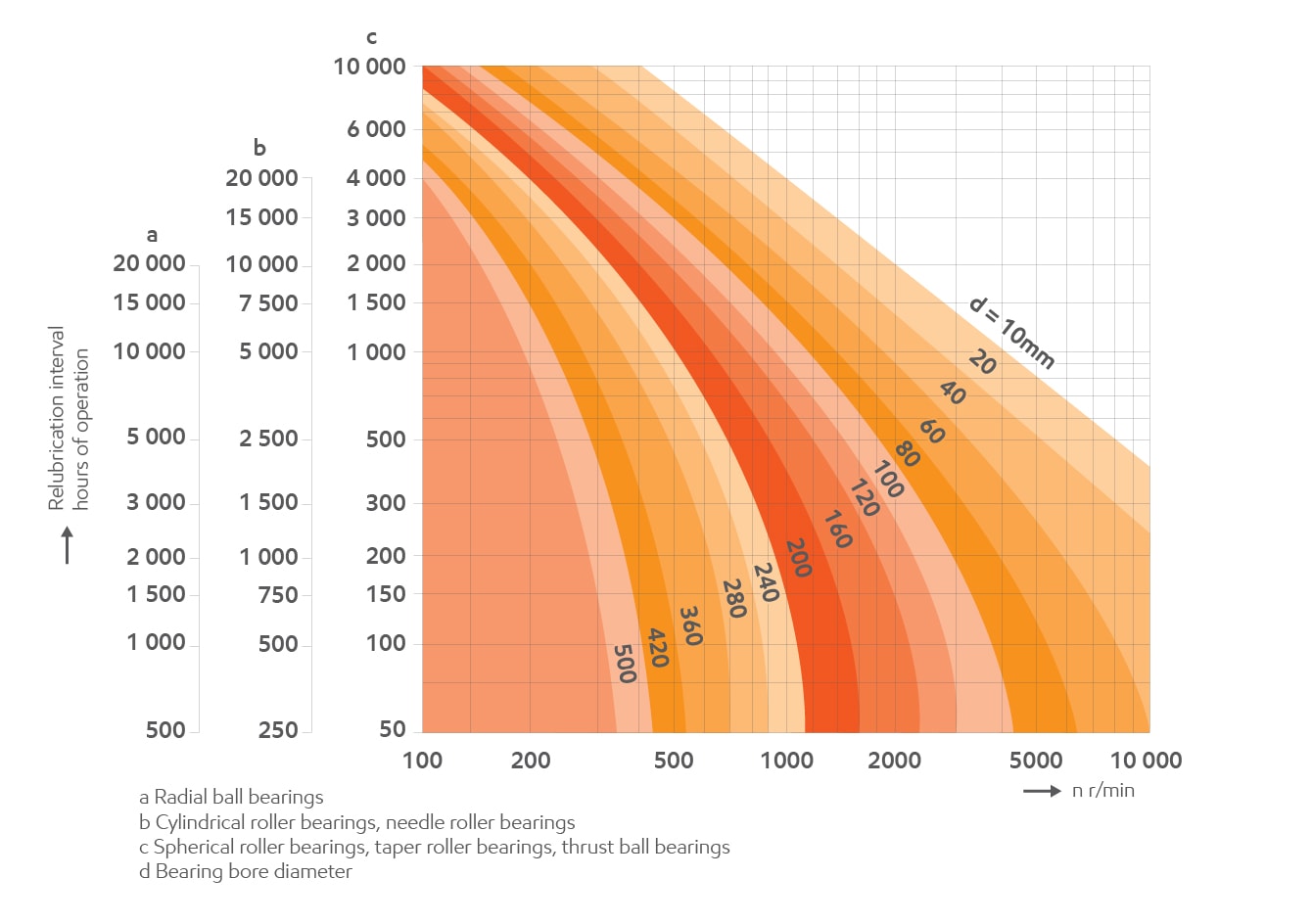
For bearings on vertical shafts, the intervals obtained from the diagram should be halved. To account for accelerated bearing grease aging at elevated temperatures, the interval obtained from the diagram should be halved for every 2.8°C (5°F) increase in bearing temperature above 71.1°C (160°F).
Remember not to exceed the maximum operating temperature of the grease.
For larger roller bearings having a bore of 300 mm (11.8 in.) and above, adequate lubrication will be obtained only if the bearing is more frequently relubricated than indicated by the diagram, and the lines are therefore broken. Our example yields a value of 3,000 hours, or 4 months.
How much grease should I use when I relubricate?
The appropriate amount and proper regreasing interval for bearings can be calculated as follows:
G = 0.005 DB
Where:
G = weight of grease, grams
D = bearing outside diameter, mm
B = bearing width, mm
Remember, overpacking probably accounts for more bearing failures than any other single factor. If too much grease is present, internal friction will cause the temperature to rise beyond its dropping point, causing oxidation of the bearing grease and premature bearing failure.