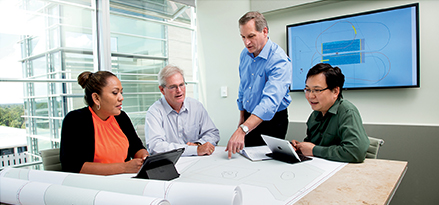
Implementing an effective lubrication management program
Across industries, maintaining safety and producing high quality products are key objectives to success. In order to realize these objectives, operators must first optimize equipment performance, beginning by implementing a disciplined lubrication management program.
Here are a few guiding principles to getting the most from your lubrication management program:
1. Understand how your lubrication program can enhance productivity.
Many people believe that simply maintaining the lube levels in their equipment provides effective lubrication, without considering that a structured lubrication management program can optimize equipment reliability, maximize return on investment and reduce overall maintenance costs.
Caption: This chart illustrates an example of the possible change in one plant’s total costs after implementing an effective lubrication management program.
2. Define the key program goals and objectives.
By defining the goals of the lubrication program, operators can ensure they have the proper tools to help get the most out of their lubrication programs.
Consider the following goals for your program:
- Apply the lubricant in the correct manner, at the proper time and in the right amounts
- Reduce lubricant-related failures
- Integrate the plant’s preventive and predictive maintenance goals into the lubrication program
3. Make sure you have the right tools and people.
Although no single program will work for all applications, there are a few tools that can help you to achieve success:
- Leadership, teamwork and communication: A successful lubrication program requires a team that communicates with all members of the manufacturing group, led by someone who can assume the responsibility to drive and control the program. Leaders should plan for continual improvement and measure their team's progress frequently.
- Training and standard operating procedures: For the program to continually improve, both the program leader and lubricators must learn lubrication best practices and new techniques. Standard operating procedures can assist in the training of lubricators and help ensure quality work by enabling program leaders to track and communicate equipment condition.
- Scheduling, planning and tracking: Even in the smallest of plants, a successful lubrication program is likely to generate a substantial amount of data. Implementing a computerized data management system can help track important equipment trends.
- Measurement and analysis: Knowing how the program is progressing is critical to understanding its effectiveness. The following metrics can help lubricators track their progress and make program-related decisions:
- Total maintenance costs and per cent spent on lubrication
- Per cent of scheduled and unscheduled equipment downtime
- Number of lubricant-related failures and safety incidents
- Per cent of maintenance overtime labour
- Total lubricant consumption
Analyzing these metrics will help validate the lubrication program and illuminate areas for improvement. Whether conducted internally or by a third party, benchmarking the lubrication program against other best-in-class operations will yield tremendous dividends.